The Grenfell tragedy shocked the construction industry and exposed the disastrous consequences that inadequate consideration of fire safety can lead to. The debate has since focussed predominantly on high-rise external cladding, but there are a whole range of common practices, and materials used, on construction sites that can lead to unacknowledged risks.
Fire safety consultant Arnold Tarling has a checklist of common culprits for the spread of fires, which are not just routinely overlooked but frequently not appreciated in the first place by the specifying design consultant or the contractor. Dry lining, double-layer plasterboard, hidden voids, unsealed penetrations in critical walls, door set installations and – popping up everywhere as everyone’s instant fix – expanding foam are just a few of the usual suspects.
Tarling will be one of the expert panellists discussing fire safety risks and responsibilities on CPD Day at Guerrilla Tactics 2018: Expanding Practice: Navigating the architecture of planning, procurement and property, which takes place at the RIBA on 13–14 November 2018.
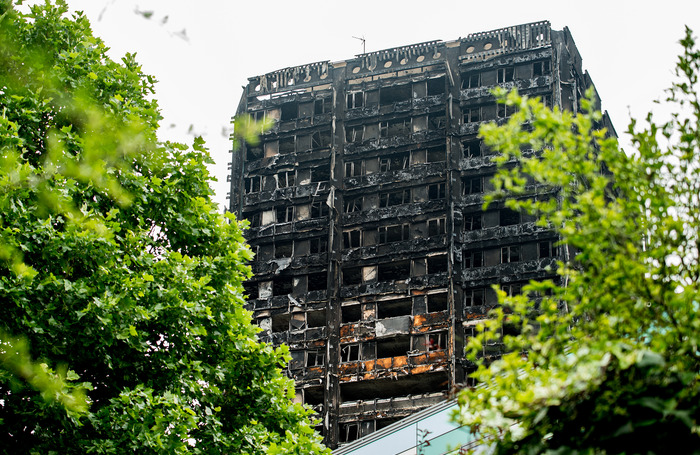
Hopes for a major step forward in fire safety have been pinned on a two-stage revision of the Approved Document for Part B of Building Regulations, with the first stage currently out for consultation and already criticised by the RIBA for its lack of ambition and its failure to introduce any significant changes.
But at the site level, Tarling argues that many of the mundane practices that give rise to common fire risks at the domestic or major project level will not be addressed by a revised Approved Document – for the simple reason that Part B depends upon everything covered by other parts of Building Regulations being carried out properly.
He cites dry lining as one good example of a widespread problem. Dry lining is supposed to be sealed with a continuous line of adhesive where a ceiling meets a wall, but generally it is not. This is because the sealing is a requirement of Part L covering energy efficiency; it is not recognised as a fire safety issue.
Traditionally, plasterboard joints would be skimmed with plaster. Now contractors looking only to satisfy Part L might use expanding foam adhesive, which is flammable, and which should not satisfy Part B.
In short, Part B does not spell out risks in instances where other regulations are supposed to ensure they will not arise.
Tarling urges architects to look beyond the letter of Part B when dealing with real-world situations on site. For instance, in properties that require protected fire-escape routes, toilets and bathrooms do not need fire doors as they are not expected to be the source of a fire. But if a bathroom is to share a wall full of plastic pipe-runs with a kitchen, there is clearly a potential risk of a fire spreading.
With adaptions or conversions, as a good practice principle the architect should think about how alterations could have an impact on things already in place.
‘In any project, the architect must understand what the critical areas are from a fire safety point of view, and how compartments within a building might be breached by construction work on site,’ says Tarling.
‘They should make sure that contractors and installers are given information on the fire performance requirements of critical walls and floors – and the need for any penetrations to be properly sealed.’
One problem that is particularly hard for architects to address is the substitution of cheaper alternative products on site. Tarling says risks can arise from something as simple as an unsupervised builder using a cheap mastic rather than the intumescent product that should be used for sealing critical gaps.
‘You can specify to your heart’s content, but at some level it will be down to the contractor to ensure that cheaper products are not being substituted. You need to make sure that at least they have all the information they need regarding fire risk.’
He points out that a good certified installer will actually want to take photos to show what they have done, and what products they have used, for their own protection. Should their work be damaged by someone else, they have evidence to show they were not at fault.
There is nothing better than a spot-check of work before it is covered up, but this is often not an option. Tarling is a great supporter of taking digital photos, and lots of them. Photos can be a useful alternative, and you can reasonably ask contractors to supply them, particularly where you want to be satisfied that cheaper products are not being substituted and that fire safety corners are not being cut.
Thanks to Arnold Tarling, Director, Arnold Tarling FRICS.
By Neal Morris. This is a Professional Feature edited by the RIBA Practice team. Send us your feedback and ideas
RIBA Core Curriculum Topic: Legal, regulatory and statutory compliance.
As part of the flexible RIBA CPD programme, Professional Features count as microlearning. See further information on the updated RIBA CPD Core Curriculum and on fulfilling your CPD requirements as an RIBA Chartered Member.
Posted on 25 October 2018.