Keeping up with innovations in concrete is literally a full-time job for Elaine Toogood, senior architect at The Concrete Centre. After two thousand years of use, new variations of the material seem to arrive faster than ever.
Toogood is keen for architects to take a rapid tour of some of the latest innovations at the 70 Years of Concrete Quarterly exhibition at The Building Centre in London.
The basic concrete mixture of around 10% cement plus aggregates has a remarkable capacity to respond to changing agendas. Toogood points to new porous concrete mixtures developed for sustainable drainage systems (SuDS), basically a reworking of the no-fines concrete idea to address flooding risk.
Addressing sustainability continues to be a work in progress. Toogood is a member of the RIBA Sustainable Futures Groups and says there is far more understanding among architects of the sustainability role that concrete can play than there used to be. Manufacturers meanwhile have also been driving down their own carbon footprints, with a 60% overall reduction since 1990.
Much of the sustainability interest in concrete revolves around its use as thermal mass, and more recently whole-life costing as, of course, concrete is a very long-lasting material.
What is not so widely appreciated is the ready availability of low-carbon, or ‘green concrete’.
‘Pretty much any type of concrete can have its carbon footprint brought down through specification. Structural engineers know all about the options, architects simply have to ask for them,’ says Toogood.
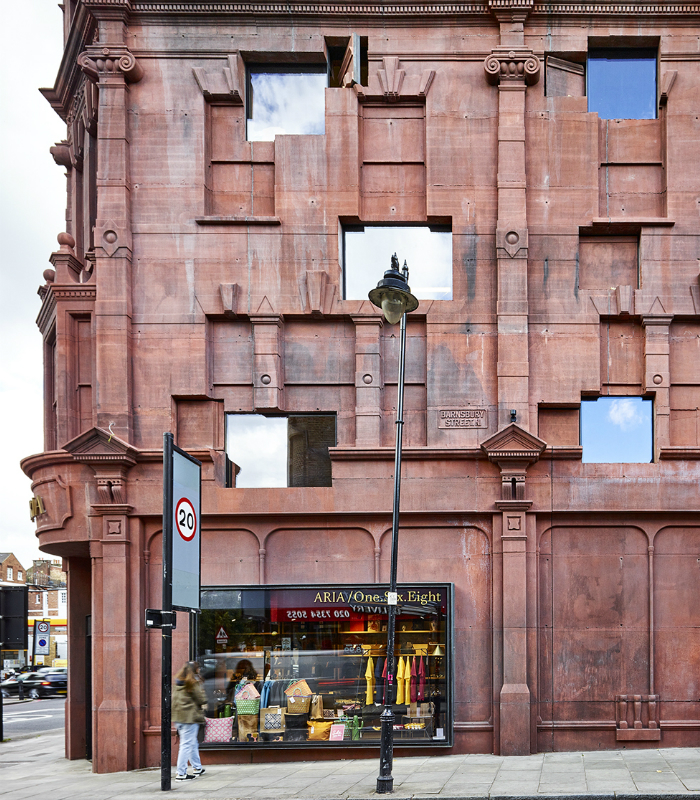
The options are cementitious additives – replacements that can be used in combination with smaller amounts of Portland Cement – such as fly ash, GGBS (ground granulated blast-furnish slag) and limestone. Generally their only drawback is a longer curing time on site, so they have been less used by contractors. The Concrete Centre has a guide to Specifying Sustainable Concrete.
Toodgood explains that alternative cements, or novel cements, that offer low-carbon alternatives to Portland Cement, are already available and are likely to become familiar over the next decade. However, they are not yet available at a large scale and will need to develop a track record of safety and durability then be incorporated, over time, into industry standards.
The specification document PAS 8829:2016 [AT1] for some forms of concrete using alkali-activated cement binders is seen as a significant step forward and there is some excitement in concrete quarters over a revised British Standard expected next Spring that will support the use of some cementitious replacements.
‘There is a lot of innovation around the recipes and ad-mixtures for concrete that offer new qualities, such self-compacting concrete that flows and compacts under its own weight and is good for use where there are embedded services,’ says Toogood.
One example of the use of self-compacting concrete is Zaha Hadid’s Aquatics Centre. Visitors to 70 Years exhibition can also see an element of its concrete diving platform showing off the double-curvature shaping of concrete that digital technology now allows.
Increasing use of concrete for thermal mass will inevitably lead to more exposed concrete, but it’s not going to be flat and grey this time around. Great strides have been made in pigmented concrete, texturing and surface finishes and now graphic concrete techniques so good they can achieve photographic effects.
Toogood recommends a visit to the website of Finnish pioneer Graphic Concrete to see what can be achieved. This company takes any image and prints it on a membrane with a surface retarder that can be sent to your local concrete prefabrication company. When the retarder is washed off the cast concrete, the image is revealed. There is no limit to the scale, you can effectively print whole building facades.
Another innovation just arrived is the use of coloured pigments in ready mix concrete. Difficulty in achieving colour consistency has held back the use of pigmented concrete, but recent advances in digital pigment dosing that takes place in the mixer en route to the site means that casting in-situ coloured concrete is now an option.
Amin Taha + Groupwork’s just-completed project for Aria in London’s Islington, has entire, meticulously-detailed Victorian façades – part accurately recreated from the mirror building across the street, part deliberately ‘mis-remembered’ through misplaced formwork – cast in situ in terracotta/concrete.
It’s a technical triumph of CAD modelling and polystyrene formwork, but Toogood points out that the cast cavity shell structure also made good use of the new pigmented ready-mix.
She adds that any architect with a ‘How did they do that?’ enquiry about an innovative use of concrete they have seen can contact her at The Concrete Centre for answers.
The 70 Years of Concrete Quarterly exhibition at The Building Centre, Store Street, London, runs until 30 October 2017.
Thanks to Elaine Toogood, senior architect, The Concrete Centre.
Text by Neal Morris. This is a ‘Practice News’ post edited by the RIBA Practice team. The team would like to hear your feedback and ideas for Practice News: practice@riba.org.
Posted on 14 September 2017.